WarpSPEE3D Installation Complete
With construction still progressing at the Neighborhood 91 location, HAMR is excited to announce that the installation of their new WarpSPEE3D system has been completed! Copper and Al6061calibration bars have been successfully printed and the system is now ready for operation. The system will continue to be calibrated for a host of different alloy and composite systems encompassing ferrous and non-ferrous alloys, cermets, and refractory alloy systems. HAMR’s initial work will focus on supporting ongoing SBIR/STTR and IR&D efforts towards commercial and defense needs.
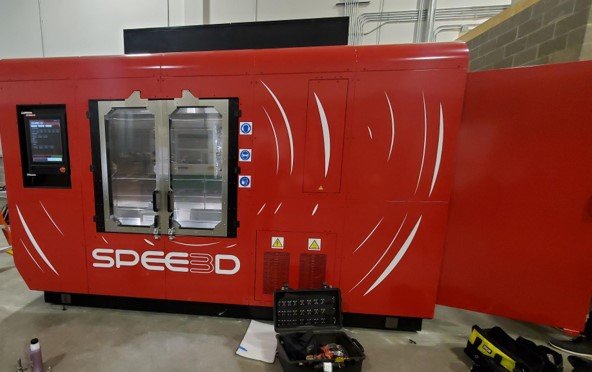
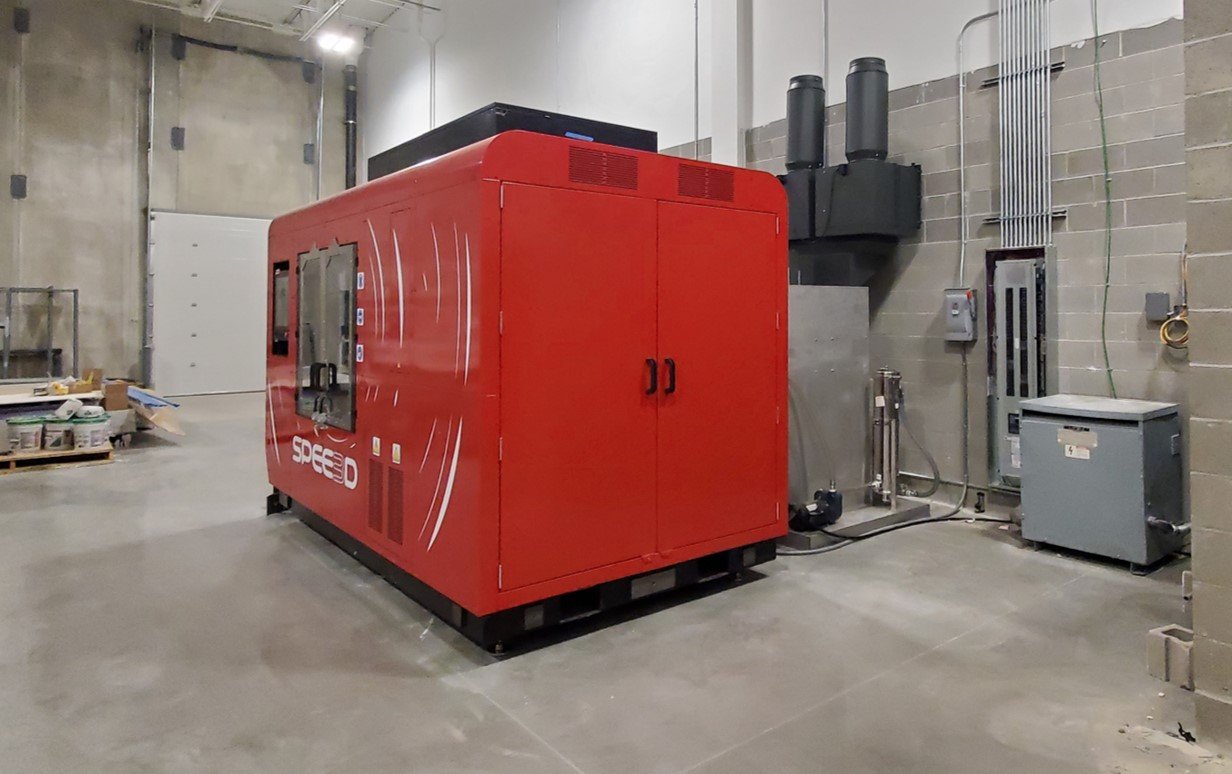
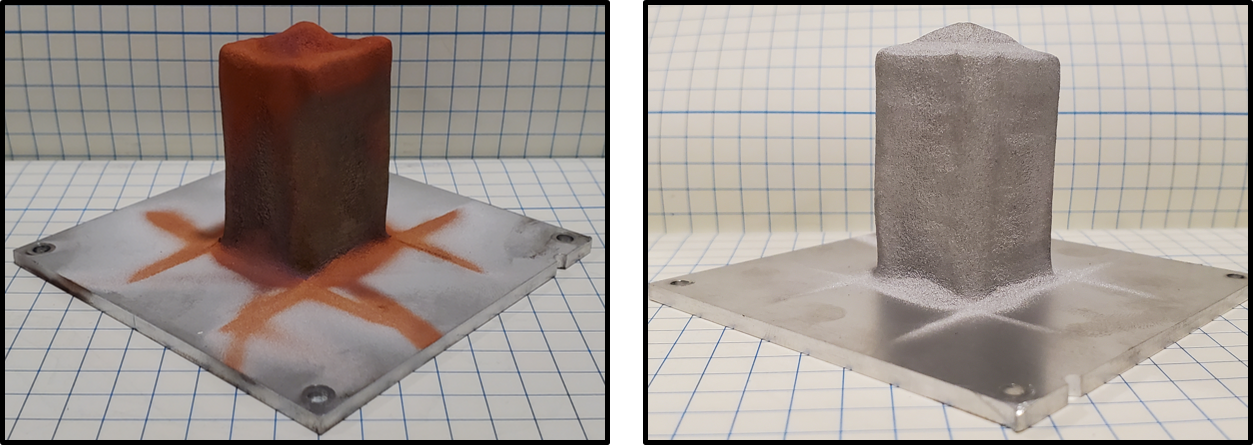
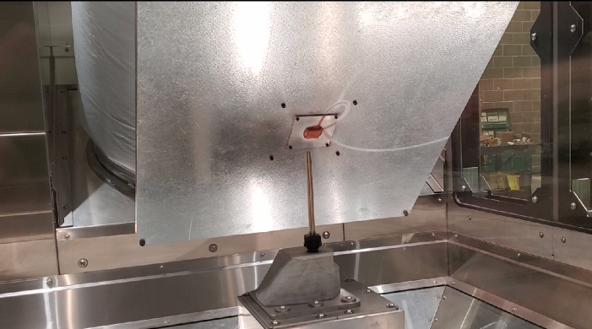
About the system: This large format cold spray additive manufacturing (CSAM) unit will facilitate the transition of cold spray repair and AM technology to commercial and government partners by providing the capability to produce full-scale parts in a rapid and affordable manner. The WarpSPEE3D system has build volume of 1.0m Ø x 0.7m and build rates on the order of 6 kg/hr or1 L/hr, providing HAMR the capability to produce large format prints and quickly iterate designs and materials to facilitate a rapid deployment to our customers. Numerous Al, Cu, Fe, Ni, Ti and Nb-based alloys have been demonstrated on this machine and will be further developed at HAMR Industries LLC.
Thrust areas: HAMR has significant experience in the cold spray arena, particularly in development of corrosion resistant materials. Initial interests lie in utilizing this system for applications ranging from R&D to industrial implementation and DoD sustainment efforts. In the R&D space, HAMR is focused on expanding the library of demonstrated materials for cold spray and CSAM, with particular emphasis on materials for extreme environments in aerospace, hypersonics, space, and nuclear. Outside of materials, the CSAM process will be developed towards functional grading, composites, surface repairs, and collaborative robotic-autonomous processing.
For industrial and DoD sustainment applications, CSAM provides a unique capability for rapid fabrication of large and/or complex parts, economically, and with properties equivalent to that of legacy fabrication methods. With a growing catalogue of available alloys, this provides an avenue for customers to replace casting and forging applications. This is particularly important for mission-critical parts which cannot absorb the delays incurred by developing or swapping to new tooling and dies. Moreover, CSAM provides a solution when the volume of parts is low. Traditional fabrication has large up-front costs for every new part, resulting in a desire to maximum part volume to provide reasonable part costs, while one-off or low-volume custom parts tend to be too costly and impractical. Additive manufacturing is well suited to iterative design, and CSAM is one the fastest AM techniques available. With these capabilities, HAMR will be well positioned to meet the needs of industrial and defense partners who wish to bolster supply chain.
As with all programs, HAMR is always interested in building new relationships. If you or your organization have an interest in exploring CSAM for your customers or end use application, please contact us!
04/24/2023 - An earlier version of this article listed a 10 kg/hr build rate, which has been changed to 6 kg/hr.